Your Go-To Resource for ADU Expertise: Explore USModular’s Blog
Explore our series of blogs that cover every aspect of the prefab manufactured home & ADU industry. When you’re ready to start building, fill out our short online questionnaire, and we’ll contact you.
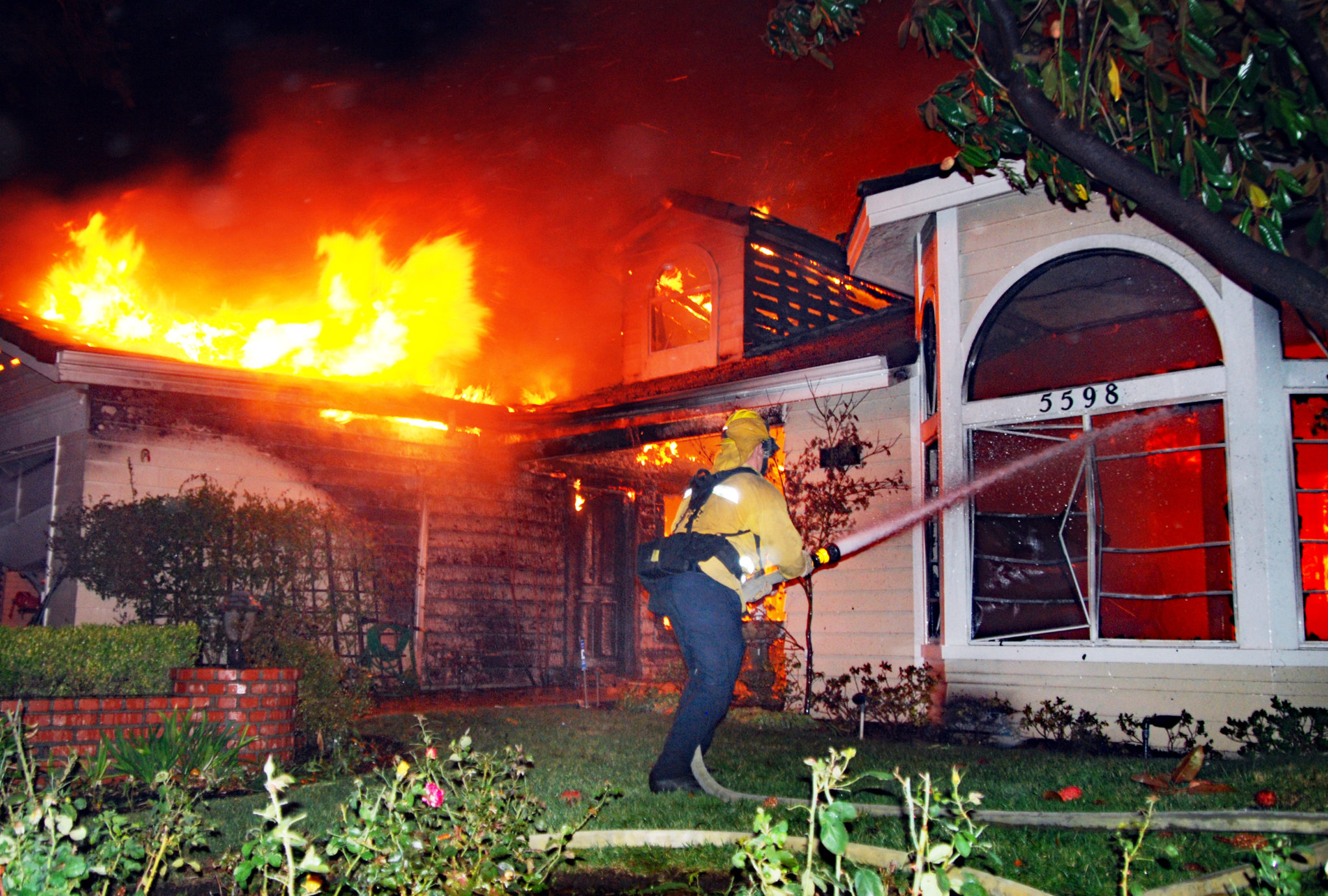
Rebuild After the Los Angeles Wildfires with Prefab Homes: A Guide to Prefabricated Construction
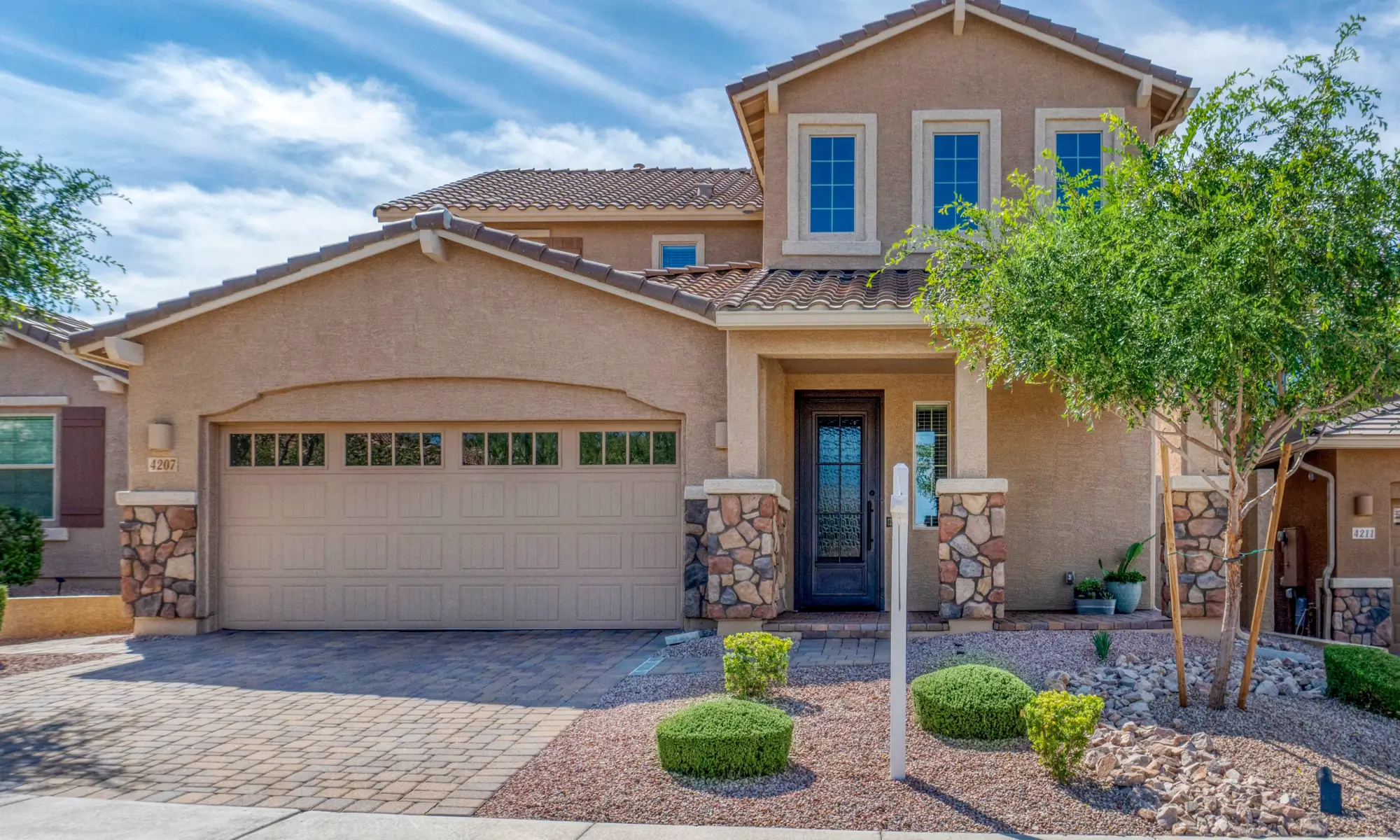
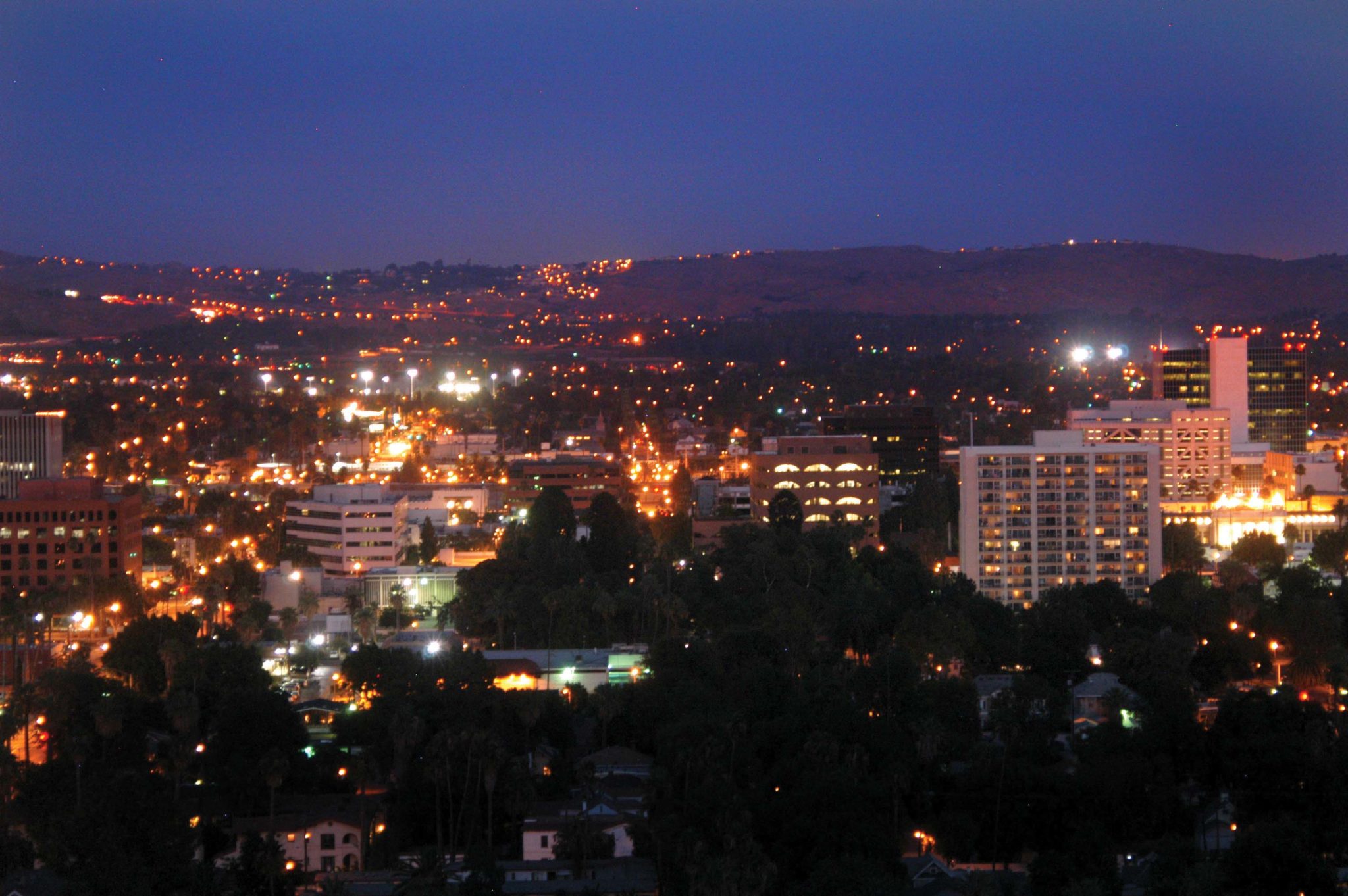

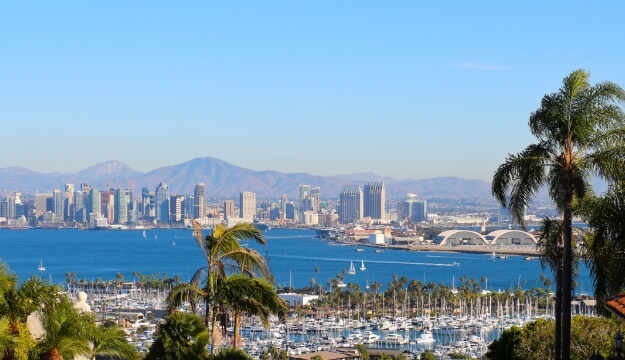
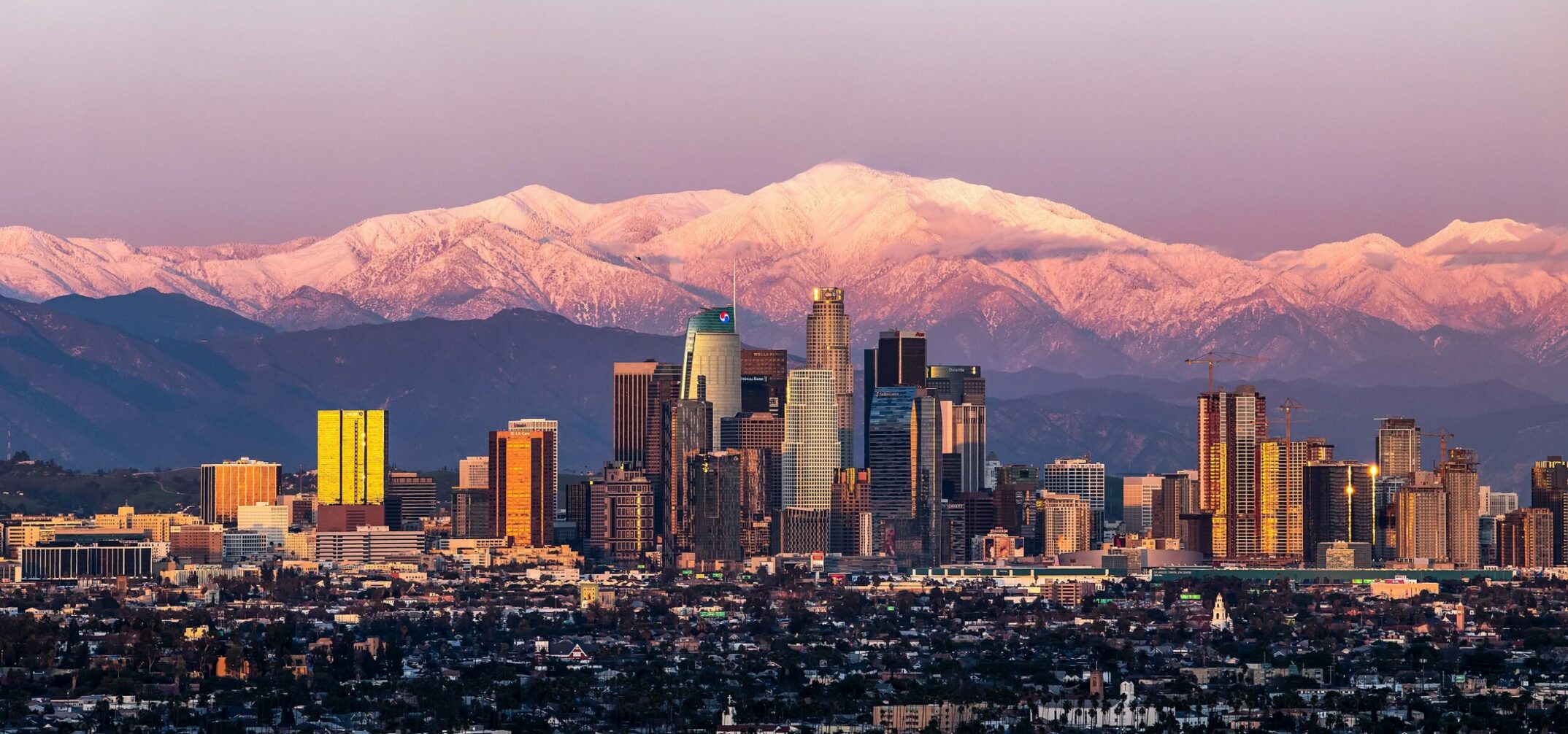

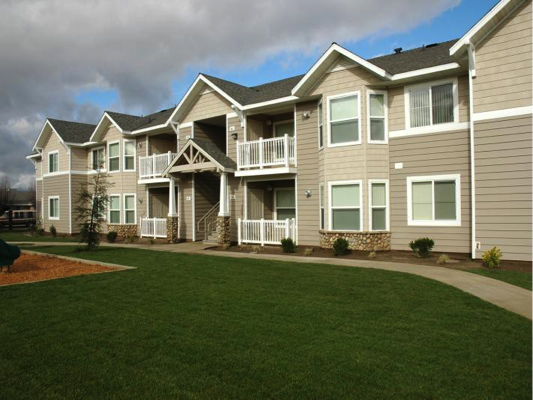
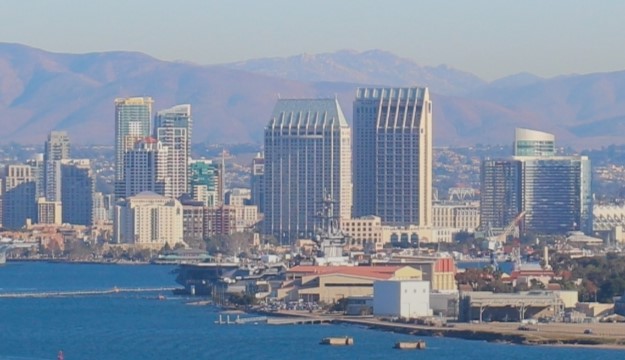
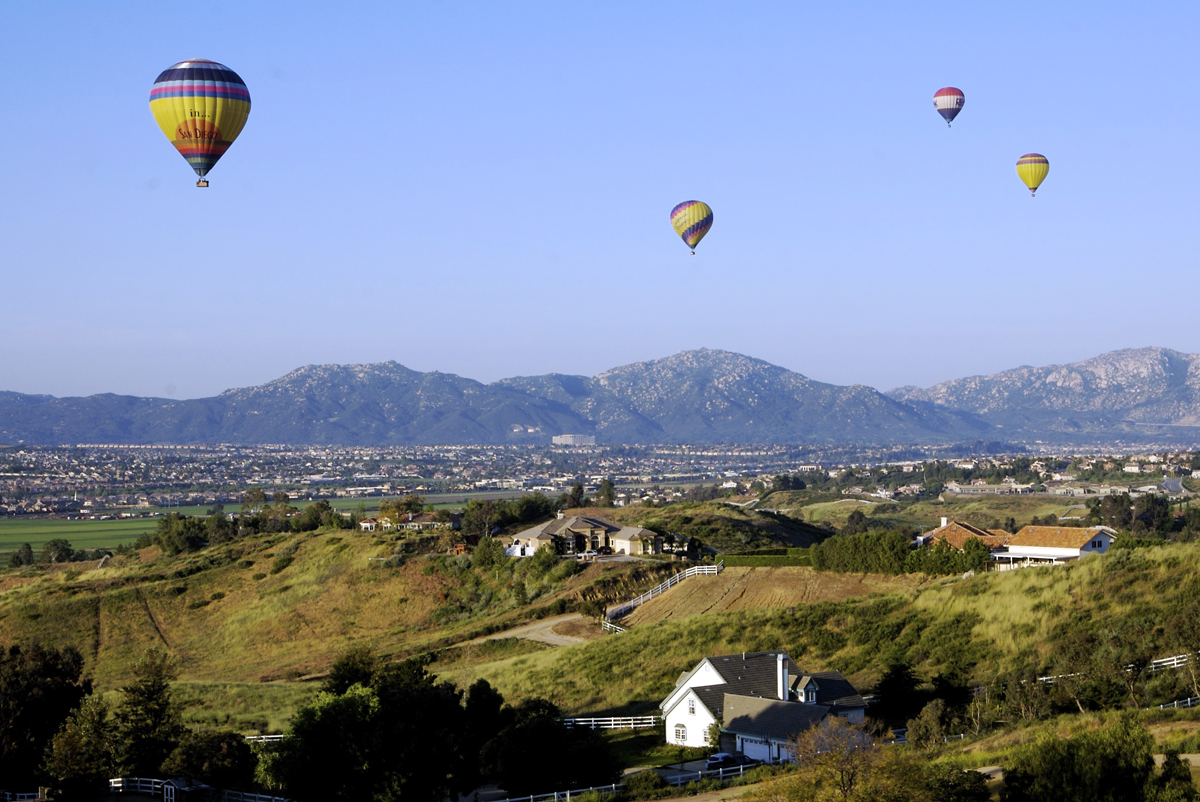
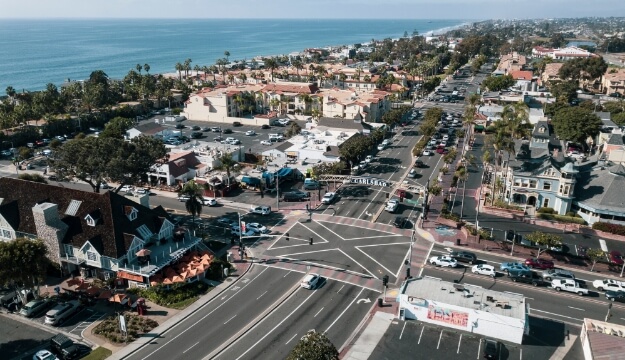
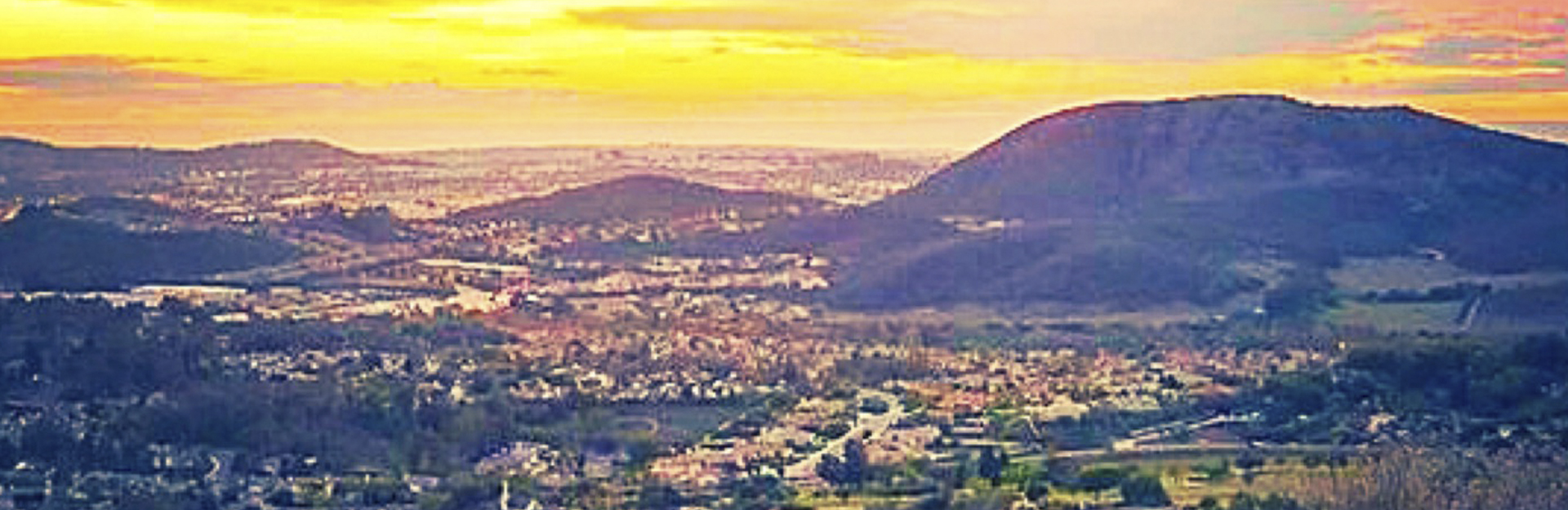
Browse our Blogs By Category

ADU Builder’s Guide to Prefab ADUs vs. Modular Homes
Southern California property owners are increasingly turning to prefabricated accessory dwelling units as diverse housing solutions. Prefab ADUs are similar to modular homes, but there are important distinctions between the two.
Understanding the Key Differences Between ADUs and Modular Homes
The most notable distinction between ADUs and modular homes is their intended purpose and how they work with your existing property. ADUs are smaller — typically ranging from under 400 to 1,200 square feet — and designed to complement an existing primary residence. Popular uses include:
- Rentals
- Extended housing for families
- Workshops
- Private guest homes
- Offices
Modular homes, on the other hand, are full-scale standalone residences built in a factory and assembled on-site on a permanent foundation. Modular homes are subject to the same zoning and permitting requirements as traditional homes.
Comparing Costs
ADUs generally have a lower price tag because they are smaller and have a more streamlined approval process. In areas like San Diego and Riverside County, construction costs range from about $150,000 to $300,000, depending on the size, design, and features.
Modular homes are larger constructions intended as primary residences. They cost between $300,000 and $600,000, and there are additional expenses to buy and prepare the land.
How a Prefab ADU Can Add Value to Your SoCal Property
Smart SoCal homeowners are taking advantage of sky-high property prices and housing demand by building an ADU to make the most of their real estate. Beyond functionality, ADUs are excellent investments that can significantly boost your property’s value and earning potential.
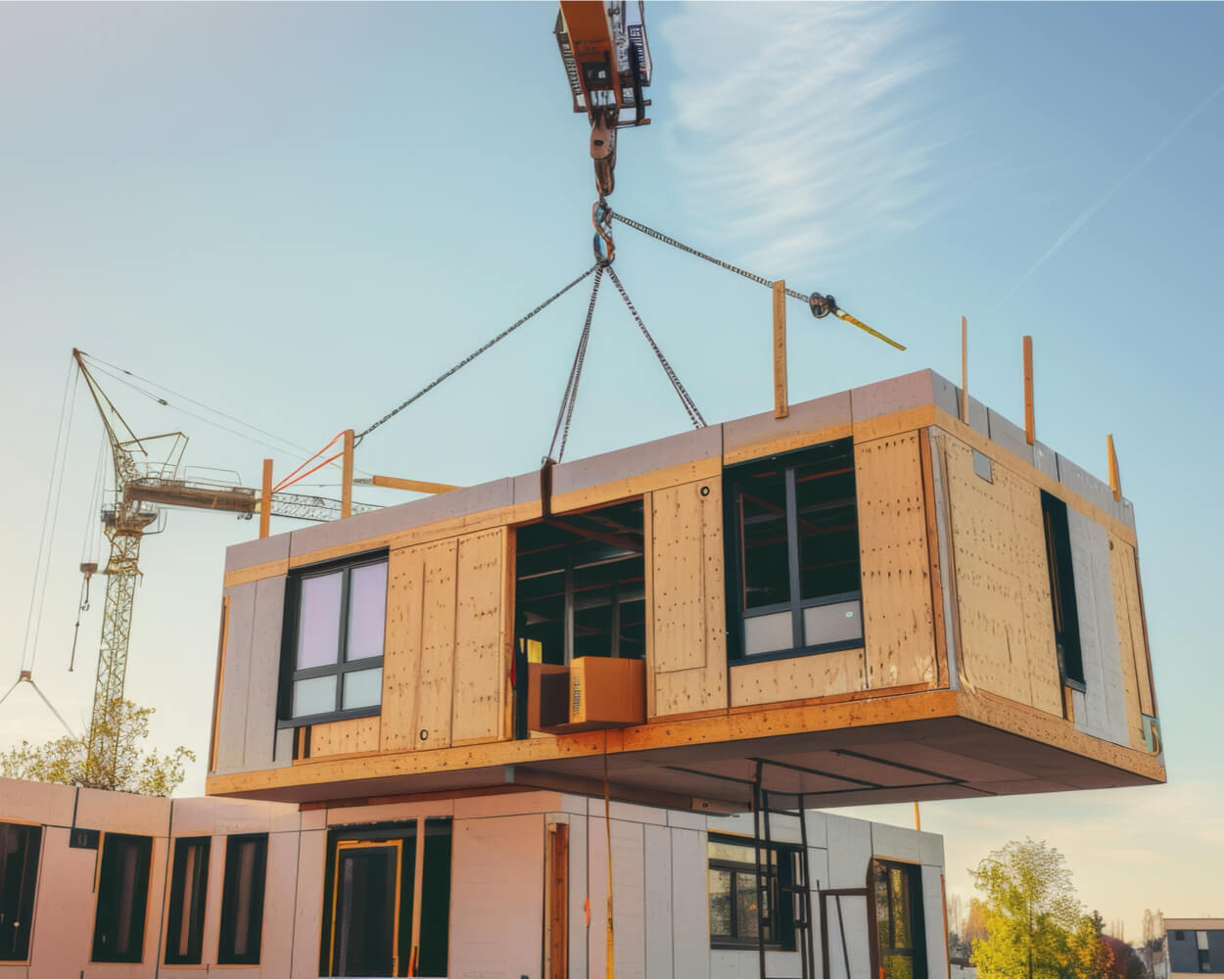
Increased Property Resale Value
Real estate professionals consistently highlight the marketability of properties with ADUs. Having an additional self-contained living space appeals to multigenerational families and rental income investors alike. It doesn’t matter what you’re using it for; an ADU makes your home stand out as it offers buyers the potential for future income or expanded living space.
Passive Income Opportunities
Southern California’s ongoing housing shortage means high demand for rental units, and a well-designed prefab ADU can generate passive income without significant lifestyle changes.
In 2023, California lowered the requirements and streamlined the approval process for ADUs. It’s now easier to earn a reliable revenue stream that helps offset mortgage payments or pay other expenses.
Enhanced Curb Appeal
An attractive ADU signals quality and care and adds to your property’s desirability and prestige in the local market. USModular’s ADU design and build solutions incorporate sleek, stylish architecture that complements your primary residence. By carefully selecting exterior finishes, landscaping, and design elements, you can create a cohesive look that boosts your home’s curb appeal.
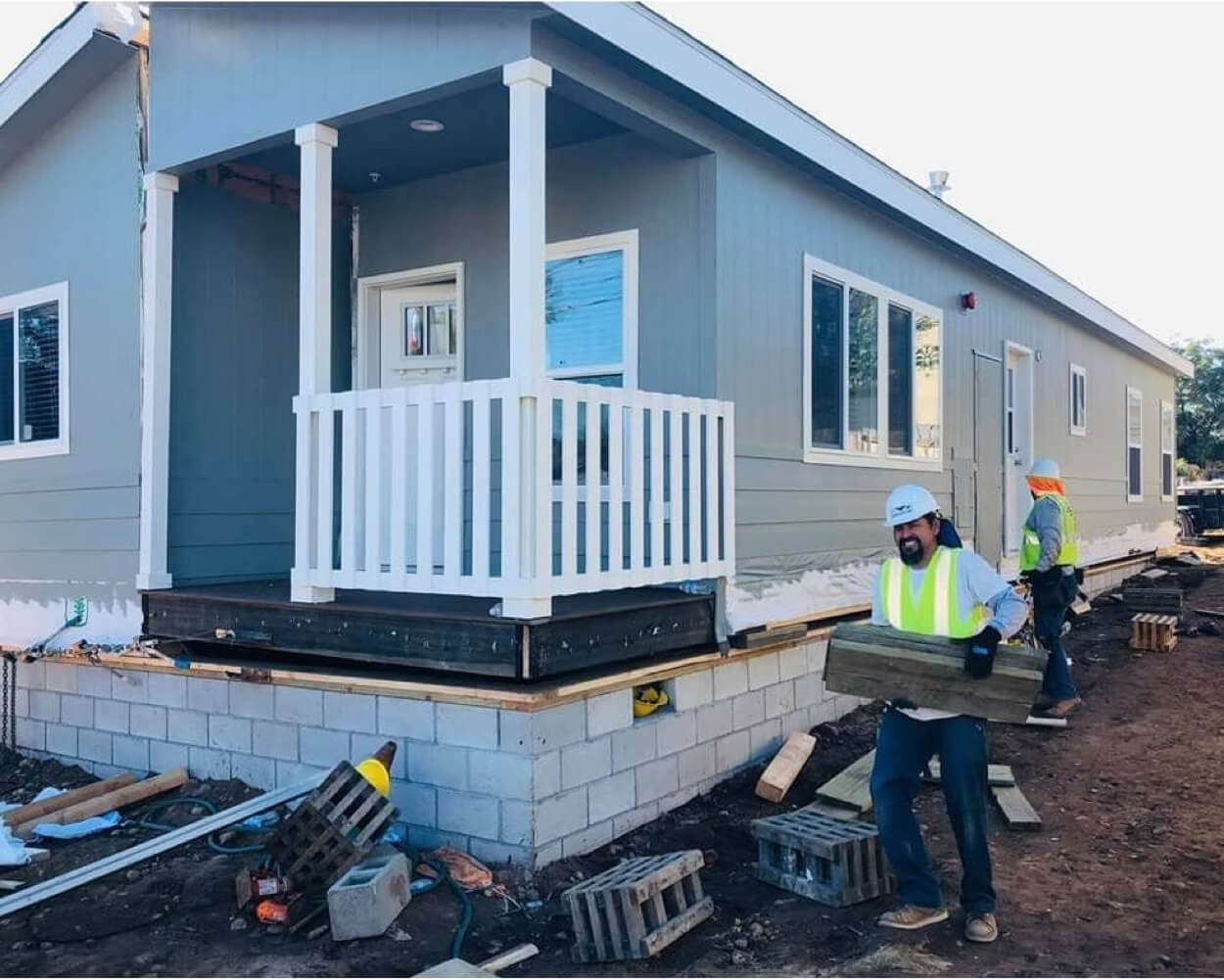
ADU Solutions for Multigenerational Living
Whether you have a young adult seeking affordable independence or older relatives needing caregivers nearby, ADUs can bring family members together. Flexibility, cost-effectiveness, and ease of construction make prefab ADUs especially popular and an ideal choice for accommodating both immediate and extended family members. You can tailor an ADU design to meet your unique multigenerational needs and build upon your connection while respecting privacy and autonomy.
Privacy and Shared Space Customization
An ADU provides a self-contained living area with its own kitchen, bathroom, and bedroom — you could literally go for weeks without seeing your loved one. This separation is very important, especially for aging parents who still value their ability to stay independent. However, you can still place your ADU near your patio or garden so that you can gather as a family without giving up any privacy.
SoCal Zoning Challenges
Navigating SoCal’s zoning laws can be a challenge. Regulations often dictate where ADUs can be built, how large they can be, and the specific requirements for utilities and parking. Fortunately, many cities in the region have relaxed restrictions to encourage ADU construction.
Working with a knowledgeable modular home builder in California, like USModular, can make all the difference. We can guide you through the legal and logistical aspects of adding an ADU to your property.
Enhanced Curb Appeal
An attractive ADU signals quality and care and adds to your property’s desirability and prestige in the local market. USModular’s ADU design and build solutions incorporate sleek, stylish architecture that complements your primary residence. By carefully selecting exterior finishes, landscaping, and design elements, you can create a cohesive look that boosts your home’s curb appeal.
Small Space Design Tips for Your Prefab ADU
Since prefab ADUs are smaller than traditional homes, you need some thoughtful design elements to create a space that feels open and welcoming yet functional. For example, large windows and skylights that let the sun in help maintain an airy and spacious atmosphere. The strategic placement of mirrors can also amplify the light and make the space appear larger than it is.
Open and Functional Floor Plans
An open floor plan that minimizes walls and barriers creates a sense of flow that makes your ADU feel larger. Consider designating multifunctional zones, like a kitchen island that doubles as a dining table or a workspace.
Clever Storage Solutions
Keep clutter at bay while keeping your ADU clean and open with storage solutions like:
- Tall cabinets
- Built-in shelves
- Under-bed bins
- Furniture with hidden compartments
You can get unconventional, too. Think about using the area beneath stairs or installing pull-out drawers in unused corners.
Multi-Purpose Furniture
Multi-purpose furniture, such as a sofa bed or a fold-out desk, is a game-changer. Using items with more than one use allows you to make the most of your small space while keeping it practical and comfortable. The theory behind developing a stylish and functional area is choosing pieces that improve the overall aesthetic while adding value to the space.
USModular Is Your Single Resource for Everything ADU
You can find everything you need to know about prefab ADUs right here, from blogs and FAQs to floor plans and building process explanations.
USModular is your preferred ADU builder in Southern California. Contact us today with any questions or to start choosing options for your own construction.